End-of-life routes for bioplastics: not only biodegradation
Giulia Fredi and Andrea Dorigato University of Trento, Department of Industrial Engineering and INSTM Research Unit e-mail: giulia.fredi@unitn.it, andrea.dorigato@unitn.it
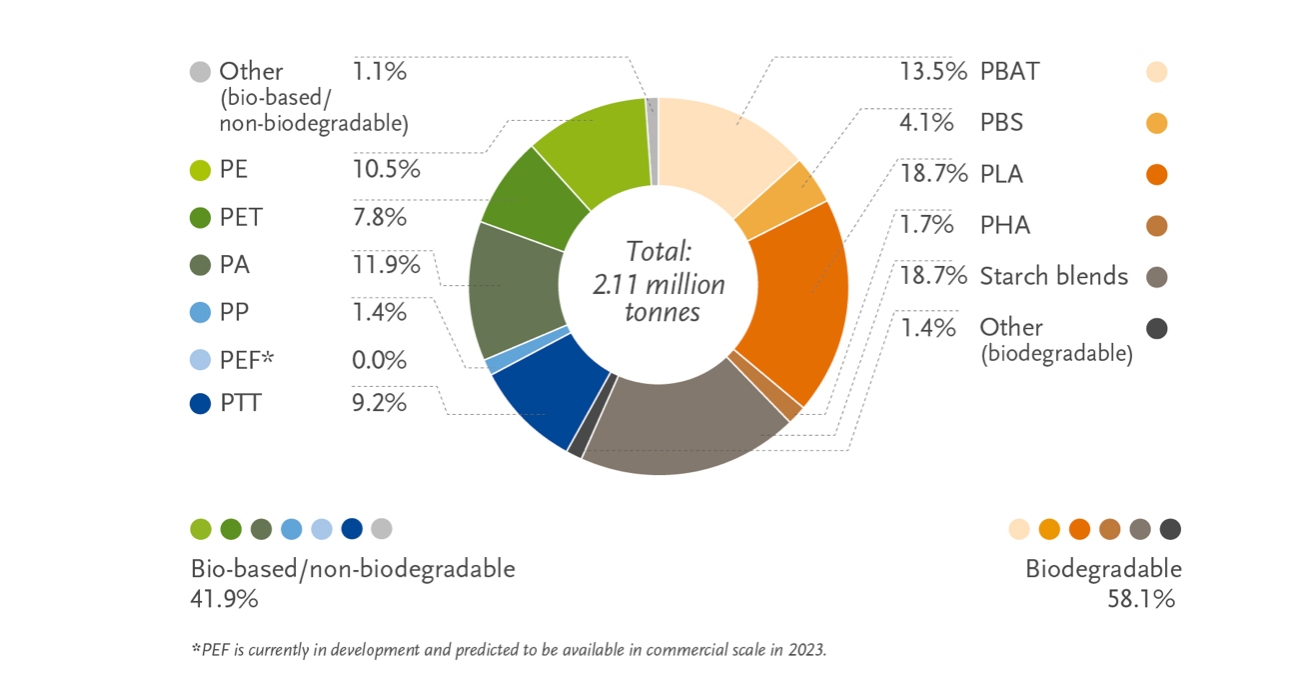
1. Introduction
Plastic materials pervade our life. Even though the industrial-scale production of plastics started only in the 1950s, they have rapidly become essential for everyday life and high-end applications thanks to their low bulk density, high durability, good processability, excellent mechanical and barrier properties, and low cost [1]. Their versatility has triggered the rapid increase in the volume of plastic produced annually over the last few decades and this quantity continues to grow. Approx. 311 million tonnes (MT) of plastic were produced globally in 2014, the synthesis of which consumed 6% of the worldwide oil production [2]. The world plastics production was 350 MT in 2017 [3] and 368 MT in 2019 [4].
However, the same properties that render plastics so useful also make the increasing amount of plastic waste, if improperly managed, a substantial environmental threat [5]. In Europe, the amount of plastic waste sent to recycling has doubled in the period from 2006 to 2018, but 25 wt% of plastic post-consumer waste (i.e., 7.2 MT) in 2018 was still sent to landfill [4]. Current projections indicate that 12 billion tonnes of plastic waste will end up in landfills or the natural environment by 2050, compared to the 4.9 billion tonnes found in 2015 [6]. Therefore, the issue of plastic waste collection and treatment, together with the non-renewable origin of most commercial plastics, has lately focused significant academic and industrial efforts towards more sustainable yet equally performing options [7].
A promising alternative is represented by bioplastics, defined as plastics that are biodegradable and/or derived from renewable resources [7-10]. Biodegradable bioplastics have alternative routes for waste disposal, thus limiting the amount of plastic waste ending up in our environment, while bioderived bioplastics allow a substantial reduction in the carbon footprint in the stage of resource extraction [11].
The intense investigation of the last few decades resulted in the commercialization of several bioplastics of industrial interest, such as poly(lactic acid) (PLA) [8], polyhydroxyalkanoates (PHAs) [12,13], poly(butylene succinate) (PBS) [14], and thermoplastic starch (TPS) [15,16], but also bio-poly(ethylene terephthalate) (bioPET) and bio-polyethylene (bioPE), which are similar to their non-renewable counterparts [17,18]. However, although bioplastics have been studied for nearly a century, their extensive industrialization is still embryonic. According to the report of the European Bioplastics Association, global bioplastic production in 2019 was 2.11 MT, i.e. only 0.6% of the total plastics production [19], and it is predicted to reach 2.89 MT by 2025 [10,20] (Figure 1). The main reasons for the limited application of bioplastics stem from the more expensive production and generally inferior mechanical properties compared to petrochemical plastics [21]. Nevertheless, as the world urgently needs an efficient alternative to petroleum-based plastics, the growth of the bioplastics market over that of petrochemical plastics is expected to be considerable in the next years.
However, replacing petroleum-based plastics with bioplastics does not necessarily solve the plastics waste issue. To increase the sustainability of bioplastics overall their whole life cycle, the increasing bioplastics production must be coupled with the implementation of effective strategies to manage bioplastic products at their end of life. Among these strategies, recycling, and mechanical recycling in particular, must play a prominent role, as it allows reducing emissions, the carbon footprint as well as the consumption of raw materials, as pointed out by many life cycle assessment (LCA) studies [22,23]. This is fundamental for all plastic products, included those made of bioderived and biodegradable plastics.
Figure 1. Global production capacity of bioplastics in 2020. (a) Total production of biodegradable and non-biodegradable plastics and forecasts; (b) production capacities by material type (reprinted with permission from [24]).
1.1. Benefits and challenges of bioplastics recycling
The life cycle of plastics, regardless of their origin and biodegradability, is truly sustainable only if the disposal options include recycling. Although everyone agrees on the convenience of recycling non-biodegradable plastics, regardless of their origin, the same is not true for biodegradable plastics, for which biodegradation is often seen as the only appropriate disposal option. However, most commercial biodegradable bioplastics (e.g., PLA and PHAs) degrade slowly under ambient conditions, even in presence of microorganisms, which may strongly limit the theoretical advantages of using bioplastics to avoid environmental pollution [19]. Biodegradation of commercial bioplastics must be performed in specific composting plants, but this should be seen as the very last life cycle step, after many steps of reuse and recycling. In fact, bioplastics disposal results in discarding valuable bioderived molecules and raw materials (e.g., lactic acid for PLA). In this optics, chemical recycling can transform waste bioplastics into alternative feedstocks for monomers and intermediate products, thereby preserving primary renewable resources and further decreasing the bioplastics’ environmental impact [19].
Furthermore, whilst bio-based non-biodegradable polymers such as bioPET or bioPE can be mixed with their petrochemical-derived counterparts and recycled in the same recycling facilities, this does not always apply for biodegradable bioplastics [25]. For example, the current plastic bottle reclaiming industry, which mainly processes PET and high-density polyethylene (HDPE), has well-established working technologies, satisfied customers, raw materials, and investors. If the current materials mix is expanded with new materials, this will require satisfying all these requirements also for those materials [26]. Biodegradable bioplastics, especially those used for packaging, are entering both the streams of plastics recycling and green-waste composting, and this could result in increased sorting cost, yield loss, and decreased processability and quality of the recycled or composted output [25]. On the other hand, implementing independent recycling streams would be subordinated to reaching a critical mass of collected bioplastics waste and to developing technologically viable, effective, efficient, and economical recovery systems and end markets for post-consumer bio-based materials [26].
In conclusion, since the bioplastics market is predicted to grow in the next years, bioplastics and conventional plastics are expected to coexist for many years to come, and it is thus essential to address the issue of recycling both biodegradable and non-biodegradable bioplastics and to study their most effective recycling pathways.
2. Classification of main commercial bioplastics
According to European Bioplastics Association, “bioplastics are either bio-based, biodegradable or feature both properties” [20]. The practical meaning of these two words, “bio-based” and “biodegradable”, is defined by international standards [3]. Biodegradable plastics are certified according to several standards defining precise conditions for composting, such as ISO 17088:2012, ISO 14855-2:2018, EN 13432:2000, EN 14995:2006, ASTM D6400-19, ASTM D5338-15, and AS 4736. For example, ASTM D6400-19 states that three main requirements must be satisfied to identify a product as compostable in municipal or industrial aerobic facilities, i.e., (i) the product should disintegrate during composting in 84 days so that a maximum of 10 % of its original weight remains after sieving on a 2-mm sieve, (ii) 90 % of the organic carbon should be converted to CO2 within 180 days, and (iii) the product should not negatively influence the ability of composts to support plant growth when compared to biowaste-derived composts not containing that product.
On the other hand, bio-based polymers, regardless of their biodegradability, are mainly certified according to EN 16640:2015, EN 16785-1:2015, ISO 16620 4:2016, and ASTM 6866-18, which measure the renewable, “young” carbon fraction through 14C measurements or radiocarbon and elemental analysis [19], although there are notable exceptions to this classification, as discussed in Section 2.1.1.2. Therefore, bioplastics can be divided into three groups (Figure 2):
- Biodegradable plastics produced from biobased resources, such as PLA, PHAs, TPS, and PBS;
- Biodegradable plastics produced from petrochemical resources, such as poly(butylene adipate terephthalate) (PBAT) and polycaprolactone (PCL);
- Non-biodegradable or partially biodegradable plastics from biobased monomers, such as bioPE, bioPET, bioPP, but also bioderived technical polymers, such as poly-trimethylene terephthalate (bioPTT) or some polyamides (bioPAs).
Figure 2. Classification of plastic materials based on their origin and biodegradability (reprinted with permission from [27]).
Among biodegradable plastics, PLA and starch blends account for the largest market share (18.7 % each) (Figure 1), while PBAT follows with a share of 13.5 %. Among non-biodegradable bioplastics, the four major players are bioPE (10.5 %), bioPET (7.8 %), bioPAs (11.9 %) and bioPTT (9.2 %) [3], while other interesting biobased non-biodegradable bioplastics are bioderived polycarbonate (bioPC), poly(methyl methacrylate) (bioPMMA) and poly(vinyl chloride) (bioPVC) [28]. Among the applications of bioplastics (Figure 3), packaging is the largest market, accounting for more than 53 % of the total weight share (1.14 MT in 2019) [19,20]. However, bioplastics are being employed in an increasing number of markets, such as the agriculture, textiles, and automotive sectors.
Figure 3. Bioplastics application by market segment (reprinted with permission from [24]).
3. End-of-life options for bioplastic waste
The best end-of-life option for any waste product depends on the material, its volume on the market, and available collection and processing infrastructure. According to the European Directive on waste management [29], waste should be managed according to a precise hierarchy indicating a priority order in the legislation and policy for waste prevention and management: (i) prevention; (ii) preparing for re-use; (iii) recycling; (iv) other recovery, e.g. energy recovery; and (v) disposal (Figure 4).
Figure 4. Waste hierarchy of the European Directive on waste management (reprinted from [30]).
Since recycling is the second-best option for waste management after preparing for reuse, the life cycle of every plastic material is really sustainable only if its disposal options include recycling. Although biodegradation can be regarded as a recycling option, and it is sometimes called “organic recycling” [31], it is normally not aimed at recovering plastic materials or monomers to be reintroduced in the life cycle of plastic products. Conversely, this is specifically the aim of other types of recycling options, such as mechanical (primary or secondary) and chemical (tertiary) recycling. For example, as long as the material quality is high, biodegradable plastics could be mechanically recycled by primary recycling, in which the recycled plastic has the same purpose as the virgin plastic, and/or by secondary recycling, in which the recycled plastic is used for less demanding applications [32]. When the material quality decreases under a certain threshold, bioplastics could be chemically recycled to recover valuable monomers that could be used as building blocks for new polymers or valuable chemicals Finally, with very low material quality, bioplastics waste could be biodegraded, when possible, and/or quaternary recycled via incineration. Therefore, it should not be a priori assumed that biodegradation is always the best end-of-life option for biodegradable plastic waste, but all available recycling strategies should be explored (Figure 5), in order to maximize the environmental benefits of these materials.
Figure 5. End-of-life routes for biodegradable and non-biodegradable bioplastic waste.
3.1 Identification and sorting
Identifying and sorting the different plastic materials composing the post-consumer waste is of fundamental importance for the subsequent recycling steps. The use of powerful and cost-effective technologies to separate plastic waste, able to guarantee high quality and purity, is necessary to produce market-competitive secondary materials [33,34]. However, the sorting step can be challenging not only because of the many types of different polymers present in the waste collection stream, but also due to the presence of compound- or layered items, constituted by different materials that can hardly be separated.
The identification and sorting steps can be performed (i) manually, on the basis of markers and labels, and/or (ii) automatically, though techniques based on differences in density, optical systems (e.g., near-infrared (NIR) techniques), fluorescent and coloring dyes, or solvents [19,35]. Manual sorting consists in the identification of different plastics by the operator on the basis of shape, color, appearance, or trademark. To facilitate manual sorting, various markers and labels could be used to identify biopolymers in the plastics waste stream. However, for instance, PLA is identified with the Resin Identification Code (RIC) “7-OTHER”, which is not accurate for the identification of an increasing fraction of PLA in the plastics waste [19]. A more reliable way to identify and separate biodegradable and compostable polymers is based on international product labels, attributed by certification organizations (e.g., European Bioplastics, DIN CERTCO) to products that meet the criteria detailed in the standards. In general, manual sorting would be still necessary at the beginning of the recycling process to remove films, paper, cardboard, and bulky items [33]. Automatic sorting techniques could be also useful to identify and separate bioplastics. For example, the differences in density between PLA (1.25-1.49 g/cm3), PHB (1.21-1.26 g/cm3), and polyolefins (<1 g/cm3) can be used to separate these materials through air classifiers or float-sink separation techniques with appropriate solvents. These density differences could also be accentuated by adding suitable additives during processing [19].
Another separation technique is near-infrared spectroscopy (NIR), which is likely the most diffused technology in plastic sorting and recycling. It is based on collecting reflected spectra of polymers in the wavelength range 700-1000 nm, and these spectra are different according to the specific polymer [33,36]. For bioplastics, NIR has been proven successful to separate PLA from PET waste, but it could be too expensive, given the current limited PLA fractions in the waste streams, and this may explain the lack of patents related to NIR sorting of bioplastics [19].
3.2. Recycling options
3.2.1 Mechanical recycling
Mechanical recycling can be defined as the processing of waste by physical means and is regarded as the main approach for plastic recovery, as it is generally less expensive, requires relatively simple technology, and has a lower environmental impact than chemical recycling [10,35]. Mechanical recycling starts with waste collection, screening, and manual and/or automatic sorting, and is composed of several steps such as grinding, washing, drying, compounding/extrusion, and granulation. These steps may also occur in a different order and more than one at a time, according to the size, shape, and composition of the feed plastic waste [33].
Mechanical recycling comprises both primary and secondary recycling. Primary recycling is a closed-loop recycling technique that can only be performed on plastic waste of high quality and known history. It is generally not related to post-consumer plastics, but to the reconversion of uncontaminated plastic waste (e.g., production scraps) into its original pellet or resin form within the same production plant, and thus it does not require sorting and cleaning [36]. Secondary recycling is the mechanical reprocessing of waste, post-consumer plastics. At the end of secondary recycling, the recycled material generally shows poorer mechanical properties than the virgin product, and therefore the recyclates are normally destined for the production of less demanding applications [10]. Secondary recycling is only economically feasible when the waste is not constituted by too many materials and/or contaminated, which would otherwise require long and expensive separation and purification steps [37].
Although mechanical recycling is a well-established recycling route for traditional plastics, its application to bioplastics should be handled with care, especially in the case of biodegradable plastics. Most of the polymers of this class, including PLA, PHAs, and polyglycolic acid (PGA), are aliphatic polyesters, and thus quite thermosensitive [3]. This problem is worsened by their high hygroscopicity, as the absorbed water favors hydrolytic breakdown of the molecular chains at high temperatures, thereby accelerating the thermal degradation. Therefore, while mechanically recycling these bioplastics, it is fundamental to accurately dry these materials before reprocessing.
Conversely, non-biodegradable bioplastics as bioPET, bioPE, or PEF can be mechanically recycled together with their non-renewable counterparts. PEF, in particular, could be introduced in the current PET waste stream in low amounts (up to 2 wt%) without compromising the final quality of the recyclates [19].
3.2.2. Chemical recycling (tertiary recycling)
Chemical recycling, also called tertiary recycling, is a steadily growing recycling route related to the transformation of waste products into useful chemicals, such as monomers and/or oligomers re-introducible in the polymer value chain and re-used for polymerization [21]. For biopolymers, tertiary recycling is performed particularly on aliphatic polyesters, which are depolymerized in a controlled way with the main aim of saving primary resources, rather than reducing the amount of waste generated by slowly degrading biopolymers. Compared to mechanical recycling, some chemical recycling techniques (e.g., pyrolysis) can be performed also on low-quality, heterogeneous, degraded, or contaminated plastic waste and convert it into high-added-value chemicals, with the further advantage of enabling a truly circular economy of polymer products. On the other hand, it generally requires higher temperatures and is more energy-consuming. Chemical recycling can be performed through dry-heat depolymerization techniques (e.g., pyrolysis) or solvolysis methods (e.g., hydrolysis, alcoholysis) [22,38].
3.2.2.1. Pyrolysis
Among chemical recycling routes, pyrolysis is one of the most promising methods for plastic waste that is difficult to be mechanically recycled or depolymerized. It can be performed at considerably lower temperatures than incineration and does not require as many pre-treatment steps as mechanical recycling [37].
Pyrolysis is the degradation by heating plastic waste in an oxygen-free atmosphere at moderate temperatures (300 to 700 °C). The degradation of polymer chains into smaller and less complex molecules results in solids (char), gases (non-condensable substances), and also liquids (condensable vapors or oils) that can be converted into high-added-value chemicals. The relative yields of these products are determined by the process conditions and feedstock composition, and the proximate analysis is a very useful tool to assess the feedstock composition in terms of volatiles, fixed carbon, and inorganic waste (ash). Since the volatile fraction of all synthetic plastics is very high (97-99 %) and the ash content is low (1-3 %) [37], plastics can yield a very high amount of oils ( > 90 wt%). On the other hand, the yield of this process can be decreased by additives such as fillers, flame retardants, plasticizers, and dyes, which increase the char fraction.
Pyrolysis is a well-established route for polyolefin waste, yielding small hydrocarbons, but also for polymers as polystyrene (PS), poly(methyl methacrylate) (PMMA), PET, and PA, yielding styrene, methyl methacrylate, terephthalic acid, and ɛ-caprolactam, respectively. Biodegradable aliphatic polyesters can also be suitably treated by pyrolysis. For example, pyrolysis of PLA results in its depolymerization and obtainment of lactide [19].
However, the reaction has a low monomer yield and is very slow, and thus it must be performed at high temperatures (300-600 °C) and in presence of a catalyst. The high temperature may promote undesired side reactions, such as lactide racemization, thereby hindering the attainment of high-quality products. Some solutions involving special catalysts that lower the reaction temperature, such as metal oxides and hydroxides like MgO, CaO, BaO, and Al(OH)3 [37,39], have been recently proposed.
3.2.2.2. Solvolysis
Solvolysis refers to all depolymerization and partial depolymerization techniques involving a solvent, sometimes coupled with heat. Common solvolysis techniques are hydrolysis, alcoholysis, glycolysis, methanolysis, acidolysis, aminolysis, and ammonolysis. The most suitable polymers are step-growth polymers such as polyesters, polyamides, and polyurethanes, for which solvolysis can be regarded as the reverse reaction to polycondensation.
Hydrolysis is composed of two steps, i.e., water diffusion into the bulk polymer and the hydrolysis reaction properly said. For low water diffusion rates, polymer degradation occurs first on the surface (heterogeneous erosion), whereas for high water diffusion rates, the polymer is subjected to homogeneous erosion. When the degradation rate in the solid-state is slow, a possible solution is a temperature increase. High-temperature hydrolysis is somewhere referred to as hydrothermal depolymerization, which may also involve high water pressure. The high temperature (above the polymer’s melting point) and pressure accelerate the degradation reaction, which can take place in subcritical and supercritical conditions either with or without oxidizing agents [21].
For biodegradable plastics, chemical recycling, and solvolysis in particular, has not been a very important end-of-life option, but it is promising from an economic and ecological point of view. For example, for PLA, obtaining lactic acid from hydrolytic degradation of PLA waste can require less energy than producing it from biomass fermentation [3,38].
3.2.3 Enzymatic and microbial recycling
Enzymatic and microbial depolymerization are new promising techniques that harness the action of enzymes and microorganisms to degrade biodegradable bioplastics in a selective and controlled way, with the aim of recovering monomers and other valuable chemicals. This aim is what makes this technique a truly recycling method, thus distinguishing it from biodegradation and compositing, which are instead disposal methods. Enzymatic and microbial recycling could be listed among the chemical recycling techniques, but since they are relatively new methods, they are discussed in a separate paragraph.
Several research works and patents (Table 1) have been published on the enzymatic depolymerization of biodegradable aliphatic polyesters such as PLA, PCL, PBS, PTT, poly(butylene adipate) (PBA), using especially lipase or Proteinase-K followed by the depolymerization of the obtained oligomers. However, the technology of enzymatic depolymerization is still at the early stages. This recycling method is quite slow, especially for highly crystalline polymers with high intermolecular forces, and the reaction kinetics cannot be enhanced by increasing the temperature, not to degrade the enzymes [19].
3.3 Degradation and disposal options
Degradation and disposal options differentiate from the recycling options discussed so far because the main aim is to eliminate waste rather than to recover polymers or monomers to be reintroduced in the plastics value chain. Besides the degradation and disposal options suitable for conventional plastics and non-biodegradable bioplastics, i.e., quaternary recycling with energy recovery and landfilling, biodegradable bioplastics have the additional option of biodegradation, sometimes called organic recovery or organic recycling. Biodegradation can be performed through industrial or home composting, anaerobic digestion, or biodegradation on agricultural land, among which industrial composting is the predominant option. The time to complete the biodegradation depends not only on the chemistry and microstructure of the specific bioplastic, but also on the chosen end-of-life route and the biotic and abiotic factors such as the temperature, oxygen, and moisture concentration, and population of microorganisms.
3.3.1 Biodegradation or organic recovery
Biological waste treatments are end-of-life options peculiar to biodegradable plastic, and they can be performed either aerobically (with oxygen, e.g., composting) or anaerobically (without oxygen, e.g., anaerobic digestion). Composting is performed by fungi, bacteria, and actinomycetes either at low temperature (<35 °C for home composting) or at higher temperature (50-60 °C for industrial composting). It is important to note that compostable plastics are a subcategory of biodegradable plastics. Compostable plastics, such as PLA and TPS, decompose in a relatively short time under composting conditions, while for biodegradable plastics the biodegradation may be slower. Hence, all compostable plastics are biodegradable, while not all biodegradable plastics are compostable [3]. Anaerobic digestion is performed by bacteria – not fungi – either at low temperature (<35 °C for mesophilic digestion) or at higher temperature (50-60 °C for thermophilic digestion). Anaerobic digestion converts organic matter into three main substances, i.e., biogas, rich in methane and used as a fuel, biosolids, i.e., microorganisms grown on the organic matter, and liquor, i.e., dissolved organic matter, both used as fertilizers.
Biodegradation rate is very dependent on the degradation technique and environment, being faster in compost, followed by soil, fresh water, marine water, and finally landfill, since biodegradation is faster at higher temperatures and in the presence of fungi, which are active only in compost and soil environments. Moreover, not all biodegradable plastics degrade in all biological degradation environments, so the correct biodegradation route must be chosen for each type of biodegradable bioplastics [3].
3.3.2. Energy recovery (quaternary recycling)
Incineration of plastics and bioplastics waste with energy recovery, although less encouraged than recycling in the hierarchy of waste management options, can be useful to dispose of all the non-recyclable and non-biodegradable plastic waste fraction and is surely preferable over landfilling. Plastics have a high calorific value and can be used in waste-to-energy plants to reduce fossil fuel consumption [36].
Although incineration is not the desired end-of-life option for bioplastics, and biodegradable plastics in particular, they generally are made only of C, O, and H, and therefore they could be accepted into these waste-to-energy plants, also because they can have similar calorific value as conventional plastics. When biobased plastics are incinerated, they are considered to produce renewable energy [3].
4. Conclusions and future trends
Plastic materials have become essential for many everyday and industrial applications, but the non-renewable origin of most commercial plastics and the issues related to the management of an ever-growing amount of plastics waste are pressing to find more sustainable alternatives. Such an alternative can be represented by bioplastics, defined as plastics that are biodegradable and/or derived from renewable resources. Biodegradable bioplastics have alternative routes for waste disposal, thus limiting the amount of plastic waste ending up in our environment, while bioderived bioplastics allow a substantial reduction in the carbon footprint in the stage of resource extraction. However, the growing bioplastics production must be paralleled with effective end-of-life strategies of bioplastics waste. Non-biodegradable bioplastics such as bioPET, bioPE, and bioPP can be collected and recycled in the same waste management stream as their petrochemical counterparts. On the other hand, the scenario is not as clear for biodegradable bioplastics, such as PLA and PHAs, for which biodegradation is often seen as the only acceptable end-of-life option. However, biodegradable bioplastics waste could also be suitable for other waste management routes, such as mechanical and chemical recycling, which may be better from the economic and ecological point of view. In fact, they address the issue of waste accumulation while recovering valuable materials and building blocks, thereby reducing the consumption of primary resources.
Considering one of the most diffused biodegradable bioplastics, i.e., PLA, its biodegradation in environmental and marine conditions is very slow, which may result in considerable environmental pollution if PLA-based waste is incorrectly managed. Therefore, it is important to evaluate the recyclability of PLA, which must start with finding the best strategy for PLA waste collection and the opportunity to establish an independent recycling stream, to preserve the output quality of the well-established recycling pathways of conventional plastics, such as PET. Then, the best recycling route (mechanical, chemical, enzymatic) and the recycling conditions must be chosen, which may depend on several factors such as the material quality of PLA waste. Although mechanical recycling is often designated as the best recycling option from an environmental and socio-economical point of view, it is fundamental to tackle the tendency of PLA to thermally degrade during reprocessing. This can be addressed by carefully selecting the processing parameters and by a proper compounding/additivation stage, to obtain a high-quality recycled PLA with tailored properties that can easily find a market share.
The study of the best recycling route for biodegradable and non-biodegradable plastic waste must also consider the economical convenience and the marketability of the output products of every recycling strategy. In any case, since the bioplastics production is growing and such materials will coexist with conventional plastics for decades to come, it is vital to find the best end-of-life pathways for each of the most common bioplastics, regardless of their biodegradability, to promote a concrete shift of the whole plastics value chain towards sustainability.
5. References
[1] R. Geyer, J.R. Jambeck, K.L. Law, Production, use, and fate of all plastics ever made, Science Advances 3 (2017) 1700782.
[2] W.E. Forum (2016) The New Plastics Economy. Rethinking the future of plastics. Geneva, Switzerland
[3] T.M. Letcher, Plastic Waste And Recycling: Environmental Impact, Societal Issues, Prevention, and Solutions, 2020.
[4] PlasticsEurope (2020) Plastics – the Facts 2020. An analysis of European plastics production, demand and waste data. .
[5] M. Bergmann, L. Gutow, M. Klages, Marine Anthropogenic Litter, SpringerOpen, 2015.
[6] K.D. Cox, G.A. Covernton, H.L. Davies, J.F. Dower, F. Juanes, S.E. Dudas, Human Consumption of Microplastics, Environ Sci Technol 53 (12) (2019) 7068-7074.
[7] G. Guidotti, M. Soccio, N. Lotti, M. Gazzano, V. Siracusa, A. Munari, Poly(propylene 2,5-thiophenedicarboxylate) vs. Poly(propylene 2,5-furandicarboxylate): Two Examples of High Gas Barrier Bio-Based Polyesters, Polymers (Basel) 10 (7) (2018).
[8] D. Garlotta, A Literature Review of Poly(Lactic Acid), Journal of Polymers and the Environment 9 (2) (2001 ) 63-84.
[9] W. Smitthipong, R. Chollakup, M. Nardin, Bio-Based Composites for High-Performance Materials: From Strategy to Industrial Application, CRC Press-Taylor & Francis Group, Boca Raton, FL, US, 2015.
[10] F.M. Lamberti, L.A. Román-Ramírez, J. Wood, Recycling of Bioplastics: Routes and Benefits, Journal of Polymers and the Environment 28 (10) (2020) 2551-2571.
[11] E. White, R. Bassilakis, S. Nogués (2020) From the plastics present to a sustainable future: The bioplastics innovation landscape, players and market opportunities. ClarivateTM,
[12] Y.-M. Corre, S. Bruzaud, J.-L. Audic, Y. Grohens, Morphology and functional properties of commercial polyhydroxyalkanoates: A comprehensive and comparative study, Polymer Testing 31 (2) (2012) 226-235.
[13] F. Valentini, A. Dorigato, D. Rigotti, A. Pegoretti, Polyhydroxyalkanoates/fibrillated nanocellulose composites for additive manufacturing, Journal of Polymers and the Environment 27 (2019) 1333-1341.
[14] S.S. Ray, K. Okamoto, a.M. Okamoto, Structure-Property Relationship in Biodegradable Poly(butylene succinate)/Layered Silicate Nanocomposites, Macromolecules 36 (2003) 2355-2367.
[15] A. Dorigato, D. Perin, A. Pegoretti, Effect of the Temperature and of the Drawing Conditions on the Fracture Behaviour of Thermoplastic Starch Films for Packaging Applications, Journal of Polymers and the Environment (2020).
[16] A. Dorigato, G. Fredi, M. Negri, A. Pegoretti, Thermo-mechanical behaviour of novel wood laminae-thermoplastic starch biodegradable composites with thermal energy storage/release capability, Frontiers in Materials 6 (2019) 1-12.
[17] V. Siracusa, I. Blanco, Bio-Polyethylene (Bio-PE), Bio-Polypropylene (Bio-PP) and Bio-Poly(ethylene terephthalate) (Bio-PET): Recent Developments in Bio-Based Polymers Analogous to Petroleum-Derived Ones for Packaging and Engineering Applications, Polymers (Basel) 12 (8) (2020).
[18] M.H. Rahman, P.R. Bhoi, An overview of non-biodegradable bioplastics, Journal of Cleaner Production 294 (2021) 126218.
[19] M. Niaounakis, Recycling of biopolymers – The patent perspective, European Polymer Journal 114 (2019) 464-475.
[20] European Bioplastics Association. Bioplastics: facts and figure (2019). Berlin, Germany
[21] M. Niaounakis, Biopolymers Reuse, Recycling, and Disposal, 2013.
[22] D.H. Vu, D. Akesson, M.J. Taherzadeh, J.A. Ferreira, Recycling strategies for polyhydroxyalkanoate-based waste materials: An overview, Bioresour Technol 298 (2020) 122393.
[23] F.R. Beltran, G. Gaspar, M. Dadras Chomachayi, A. Jalali-Arani, A.A. Lozano-Perez, J.L. Cenis, M.U. de la Orden, E. Perez, J.M. Martinez Urreaga, Influence of addition of organic fillers on the properties of mechanically recycled PLA, Environ Sci Pollut Res Int (2020).
[24] European Bioplastics, Nova-istitute. Bioplastic materials. (2020). https://www.european-bioplastics.org/bioplastics/materials/. Accessed April 15 2021
[25] A. Soroudi, I. Jakubowicz, Recycling of bioplastics, their blends and biocomposites: A review, European Polymer Journal 49 (10) (2013) 2839-2858.
[26] D.D. Cornell, Biopolymers in the Existing Postconsumer Plastics Recycling Stream, Journal of Polymers and the Environment 15 (4) (2007) 295-299.
[27] S.A. Ashter, Introduction to Bioplastics Engineering, William Andrew, Elsevier, Cambridge, MA, USA, 2016.
[28] V. De Leo, M. Casiello, G. Deluca, P. Cotugno, L. Catucci, A. Nacci, C. Fusco, L. D’Accolti, Concerning Synthesis of New Biobased Polycarbonates with Curcumin in Replacement of Bisphenol A and Recycled Diphenyl Carbonate as Example of Circular Economy, Polymers 13 (3) (2021) 361.
[29] Directive (EU) 2008/98/EC of the European Parliament and of the Council of 19 November 2008 on Waste (2008).
[30] European Commission. Waste Framework Directive. (2020). https://ec.europa.eu/environment/topics/waste-and-recycling/waste-framework-directive_en. Accessed 24 April 2021
[31] S. Kabasci, Bio-based plastics: materials and applications, John Wiley & Sons Inc, Chichester, United Kingdom, 2014.
[32] A. Dorigato, Recycling of polymer blends, Advanced Industrial and Engineering Polymer Research In Press (2021).
[33] F. Pacheco-Torgal, J. Khatib, F. Colangelo, R. Tuladhar, Use of Recycled Plastics in Eco-efficient Concrete, Woodhead Publishing, Duxford, United Kingdom, 2019.
[34] B. Ruj, V. Pandey, P. Jash, V.K. Srivastava, Sorting of plastic waste for effective recycling, Int. Journal of Applied Sciences and Engineering Research 4 (4) (2015) 564-571.
[35] C. Aumnate, R. Kiesel, N. Rudolph, Understanding plastics recycling: economic, ecological and technical aspects of plastic waste, Hanser Publishers, Munich (Germany), 2017.
[36] E. Worrell, M.A. Reuter, Handbook of recycling: state-of-the-art for practitioners, analysts, and scientists, Elsevier, 2014.
[37] O. Dogu, M. Pelucchi, R. Van de Vijver, P.H.M. Van Steenberge, D.R. D'Hooge, A. Cuoci, M. Mehl, A. Frassoldati, T. Faravelli, K.M. Van Geem, The chemistry of chemical recycling of solid plastic waste via pyrolysis and gasification: State-of-the-art, challenges, and future directions, Progress in Energy and Combustion Science 84 (2021) 100901.
[38] V. Piemonte, S. Sabatini, F. Gironi, Chemical Recycling of PLA: A Great Opportunity Towards the Sustainable Development?, Journal of Polymers and the Environment 21 (3) (2013) 640-647.
[39] K. Ragaert, L. Delva, K. Van Geem, Mechanical and chemical recycling of solid plastic waste, Waste Manag 69 (2017) 24-58.