End of life scenarios of composite materials for wind blade technology
Prof. Andrea Dorigato University of Trento, Department of Industrial Engineering e-mail : andrea.dorigato@unitn.it
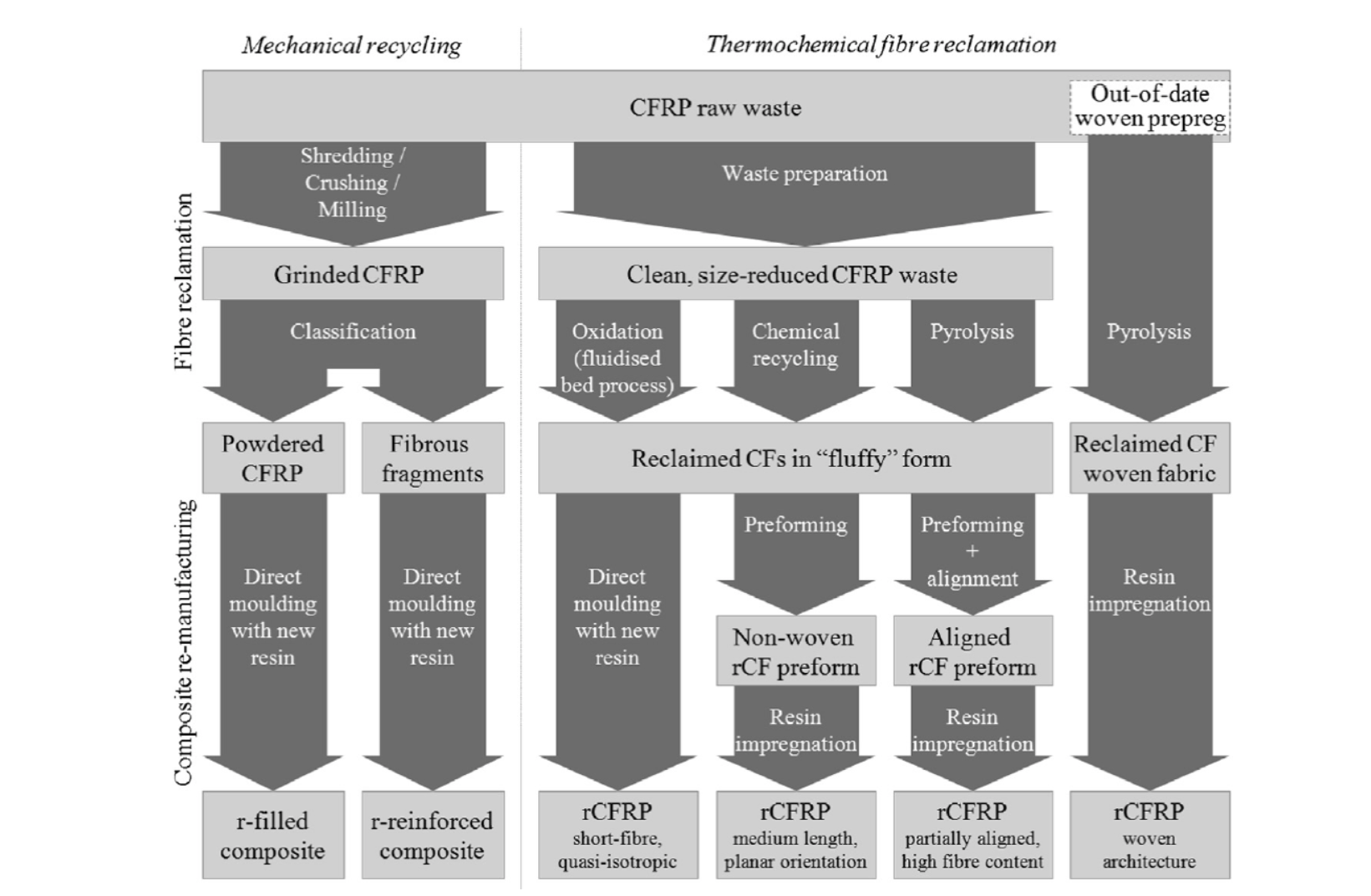
1. Composite materials for wind turbines
Wind energy is nowadays one of the energy sources with the fastest growth rate and it can thus represent a valuable and economically sustainable solution to the problems of the shortage of fossil fuels and of the climate change [1]. Basing on recent IRENA's report, in the last twenty years the worldwide wind power installed (both onshore and offshore) increased from 7.5 GW in 1997 to 564 GW by 2018. The global wind energy produced doubled between 2009 and 2013, and it represented the 16% of the renewable energy share in 2016 [2]. Generally speaking, wind turbines (WTs) can be classified in horizontal axis wind turbines (HAWTs) or a vertical axis wind turbines (VAWTs). HAWTs are nowadays the preferred turbine design, especially for big size wind projects, but small scale VAWTs have been also recently installed in urban areas, as they are characterized by lower noise levels and allow the production of energy also in locations with discontinuous and turbulent winds. Regardless to the diameter of the WT, today the greatest part of the generators is based on the Danish three-bladed rotor scheme, and large-scale power production is covered by plants having a nominal power in the range 1-3 MW. In Table 1 a classification of the wind turbines on the basis of their size, together with their applications fields, is summarized. It is evident that wind plants are rather expensive, and the economical investments on these plants are noticeably influenced by scale economies. As the specific cost of WTs strongly decreases with the plant size, high power wind towers are less expensive than small size wind generators [3,4].
Table 1. Size classification of wind turbines (adapted from [3,4])
As WTs do not produce gas emissions during their service life, wind energy is considered one of the cleanest renewable energy sources. In comparison with power plants based on fossil fuels, wind generators have considerably reduced CO, SOx, NOx and particulate emissions [5]. Unlike traditional fossil fuel resources, wind energy is practically inexhaustible. On the other hand, the specific productivity of wind power plants is rather limited, and considerable energy amounts are required for the manufacturing and the assembly of the different WT parts. Generally speaking, small-scale wind turbines are more energy intensive and have thus longer energy payback periods (between 2.4 and 4.8 years). On the contrary, big scale wind projects are characterized by very limited energy payback periods (from eight months to about one year). Therefore, it can be seen that the energetic payback time is very short with respect to the expected lifetime of a wind turbine (between 20 and 30 years).
Nowadays, HWATs blades are generally manufactured by using glass fiber and carbon fiber reinforced plastics (CFRPs). As it can be immediately seen in the mechanical properties chart reported in Table 2, the specific strength of unidirectional (UD) GFRPs (fiber volume fraction Vf = 0.5) and CFRPs (Vf = 0.6) is significantly higher than that of steel, and also the absolute strength of CFRPs is superior than that of steel. However, it has to be also considered that the mechanical resistance of FRPs is strongly affected by several factors, such as the intrinsic mechanical properties of the constituents, the interfacial adhesion conditions, the adopted processing conditions, etc. From the data reported in Table 2 it is evident that polymer composites are characterized by a superior specific strength, but the most interesting advantage in their use is probably the superior fatigue resistance. If the fatigue performance of these materials is considered in terms of specific strength (i.e. per unit weight), the advantage in the use of composite materials is further enhanced.
Table 2. Comparison of the mechanical properties of different structural materials (adapted from [6]).
2. Recycling of composite materials
As reported in Chapter 1, composite materials are endowed with unique and versatile properties with respect to more traditional materials (like metals). For as concerns their environmental attributes, the end of life scenario of composites should be analyzed in a different way with respect to commodity materials, as they are generally characterized by a longer service life, typical of structural components. The recent EU policy on waste treatment (EU 1999/31/EC and EU 2000/53/EC regulations) tends to strongly limit the negative environmental impact of waste, transforming the waste in new resources. In this sense, landfilling is the least favourable option, as the waste is not recovered and thus it does not have any value. Moreover composite materials, thanks to their elevated durability, are characterized by a very limited degradation rate in the landfilling site [7]. Nevertheless, nowadays the greatest part of the CFRP waste is landfilled, with negative environmental, economic and even legal consequences [8]. On the other hand, the effectiveness of incineration with energy recovery is strongly dependent by the composition of the composites. For instance, the organic and flammable content within GFRPs and sheet moulding (SMC) is rather limited, and the amount of recoverable energy through incineration from these materials is thus rather limited, while CFRPs are characterized by an elevated calorific value [7]. Nowadays recycling and/or reuse of composite waste is probably the best choice on the basis of the recent EU directives, while landfilling is the last option [9]. Considering the intrinsic energy intensive nature of CFRPs, these materials are ideal candidates for the application of different recycling approaches. It can be noticed that the embodied energy related to the production of 1 kg of CFRP is about 500 MJ/kg, that is 2.5 times higher than that of Al (200 MJ/kg) and an order of magnitude higher than that of steel [10]. The environmental impact of GFRPs, even if lower than that of CFRPs, is comparable to that of aluminium and much higher than that of steel. Moreover, the greatest part of the embodied energy in CRFPs is related to the production of carbon fibers and not to the polymer matrix (generally an epoxy resin). It is well known that CFs are generally produced through a high temperature treatment of different organic precursors (polyacrylonitrile, pitch, etc.), and this leads to an elevated environmental impact [11]. For instance, it was recently demonstrated that CFs recovered from waste laminates through pyrolysis have an overall energy consumption equal to 5-10% of the energy needed to produce virgin CFs.
Recycling of composite materials presents some intrinsic difficulties, mainly related to the following issues [12]:
- fiber reinforced polymers (FRPs) have a complex composition, because of the presence of the polymer matrix, the reinforcements and the fillers
- in most cases the matrix is constituted by a thermosetting resin (like epoxy), that cannot be re-melted and re-moulded
- composite materials are very often combined with other materials (metal parts, honeycomb structures etc.
Considering the importance of closing the life cycle loop of FRPs (especially in the automotive industry), different recycling approaches have been considered. As reported in Figure 1, recycling techniques can be classified as mechanical or thermo-chemical methods.
Figure 1. Overview of polymer composites recycling processes (referred to CFRPs) [12].
From a general point of view, in mechanical recycling FRPs are shredded, crushed or milled, and the resulting materials are then classified in powdered products (with an elevated content of resin) and fibrous components (rich in fibers). The recovered materials can be then used as filler or reinforcement through re-impregnation with new resin, or they can be added in asphalts and cements [13]. The resulting particulate grades are mainly utilized as filler, while the fibrous components with higher aspect ratio are utilized as reinforcement [14].
Thermo-chemical recycling consists in the recovery of the reinforcing fibers through thermal or chemical methods, and the matrix (generally with thermosetting nature) is decomposed. The fibers obtained after these reclamation processes generally possess mechanical properties comparable to the virgin ones, even if in some cases some surface defects and a deterioration of the strength has been noticed [15]. Through pyrolysis it is also possible to decompose the uncured resin in out of date woven CF prepregs and to recover the fibers. In this way, recycled carbon fiber (rCFs) can be then re-impregnated, retaining thus the original woven morphology of the prepreg (see Figure 1). In chemical recycling of composites, FRPs scraps are treated at low-medium temperature (below 350 °C) in reactive media constituted by catalytic solutions, alcohols and supercritical fluids. In this way, it is possible to collect the fibers in fluffy form, while the matrix is decomposed in oligomers that can be re-utilized as chemical feedstock for different applications [12].
Among chemical recycling techniques applied to thermosetting FRPs, hydrolysis, glycolysis, solvolysis and acid digestion are the most important ones [16]. Supercritical fluids chemical recycling methods are based on the use of substances above their critical temperature and pressure. In fact, supercritical fluids, like water and alcohol, characterized by high solubility and diffusivity, are able to decompose polymer matrix of waste composites, obtaining gas, liquid and solid products [17]. For instance, both near-critical and supercritical water was utilized to recover CFs from waste CFRPs. The resulting fibers possessed a stress at break near (> 90%) to the virgin ones, and a removal efficiency of 95% was obtained with the addition of a KOH catalyst [18]. In many cases supercritical alcohol was utilized to recycle CFRPs [19-21].
Regardless to the recycling technique, the second stage of composite recycling technology is based in the re-impregnation of the recovered fibers. The main limitation to the re-use of recycled fibers stays in their discontinuous, unsized and fluffy morphology [12]. It is thus very difficult to utilize these reinforcements for the development of structural composites. When recycled fibers are applied in direct moulding technique, they can be added to different polymer matrices through injection moulding (for thermoplastics) and bulk moulding compound compression (for thermosettings). The elevated pressure involved in these processes often leads to a substantial reduction of the fiber length, limiting thus the stiffness, the strength and the electrical conductivity (for CFs) of the resulting composites [12]. Another way to utilize recycled fibers is based on their conversion in nonwoven 2D or 3D preforms, that can be them impregnated through resin infusion or resin transfer molding (RTM). The discontinuous morphology and the random orientation of the reinforcements limit the mechanical properties of the resulting materials, that often reach a plateau at Vf = 0.3. In some cases, it is possible to align discontinuous rCFs through different techniques (like centrifugal alignment rig), obtaining rCFRPs having an elastic modulus comparable to that of aerospace-graded Al and woven CFRPs [22]. In Table 3 possible ways of reusing and apply recovered products obtained by different recycling methods are summarized.
Table 3. Reuse and application of recovered products obtained by different recycling methods (adapted from [23]).
3. Recycling of composite materials for wind blades
The structure of WTs is mainly composed by metals (steel, aluminium, copper), reinforcing fibers (GFs, CFs) and epoxy resin. Unlike glass and carbon fibers, metals are characterized by elevated recycling rates, because of their homogenous composition and their economic value. In Figure 2 an overview of the material volumes related to WTs, together with their end-of-life disposal routes, is reported [24].
Figure 2. Recycling and end of life disposal routes of the most important WTs parts [24].
Regardless to the manufacturing technique, the overall waste for producing each blade is generally around 10%, and also the consumables utilised for the infusion process (i.e. peel ply, breeding fabric, vacuum bags and vacuum tape) must be taken into account. Considering the growth rate of the utilization of the wind energy, it can be estimated that the overall amount of waste composites deriving from WTs in the next 20 years will be higher than 106 t. It is therefore clear that the end of life of composite materials should be carefully analyzed. According to the analysis reported in the book of Goodship [7], landfilling is no longer an economically feasible option for the high volumes involved, while incineration with some energy recovery can represent a near- to medium-term solution. Instead, the recovery of composite for wind blades and their recycling through different techniques could be probably the best options for the future. However, the literature scarcity on WTs life cycle assessment (LCA) studies and also the limited industrial trials clearly show that much research efforts will be required to deal with composites waste problem. The most important economic consideration that must be done when the problem of composites recycling is analyzed is whether there is a market for the recyclates. In fact, companies involved in composite waste management have to face big problems related to economies of scale and transportation costs, that can be solved only with a reliable feedstock at their disposal.
3.1 Mechanical recycling
Mechanical recycling of waste composites is probably the simpliest method, and this solution has been already scaled-up to a commercial level [25]. Mechanically shredded composites (SC) are constituted by a mixture of individual fibres, longer fibre bundles partly impregnated with resin and clusters of materials. It is therefore clear that SC quality is a key aspect for the recycling of composite parts, and that the most valuable fractions are those with an elevated long fiber concentration. The utilization of SC in new thermosetting matrices is mainly related to the possibility of limiting the amount of fibres in existing composites and reducing the cost of the product, without changing the manufacturing technique. As already said, the main limit of this technique is represented by the impossibility to obtain continuous fibers. Moreover, in some cases the intrinsic mechanical properties of the recycled fibers are considerably reduced.
A literature review of Beauson et al. was focused on the recycling of shredded composite materials recovered from WTs, utilizing rGFs for the production of new composites [26]. In that work an interesting approach, based on the reinforcement weight content, was adopted. It was highlighted that an increase of the SC concentration led to a general drop of the mechanical properties of the composites, if compared to a reference material made with only virgin fibers (see Figure 3). It was therefore concluded that a composite prepared with SC could not show better performances with respect to the corresponding composite without any reinforcement, because the reinforcing fibers were often damaged or they were not properly mixed within the new composites. Moreover, it was probably necessary to adjust and optimize the process parameters.
Figure 3. Reduction in the mechanical properties related to the amount of SC in the composite [26].
It is also possible to use mechanically recycled fibers in additive manufacturing technologies, like fused deposition modeling (FDM). In a recent paper of Rahimizadeh et al. short glass fibers from scrap wind turbine blades were recovered and mixed with a polylactic acid (PLA) matrix through a double extrusion process, to prepare novel composite filaments for FDM [27]. Composite filaments with fiber concentrations up to 25 wt% were utilized to produce 3D printed tensile specimens. The resulting samples showed an increase of the specific stiffness of the 74% with respect to neat PLA, associated to a reduction of the specific tensile strength and of the failure strain of 42% and 65%, respectively. Moreover, it was also found that PLA samples reinforced with recycled GFs had a specific modulus and tensile strength respectively 18% and 19% higher than those of samples reinforced with virgin GFs.
3.2 Thermal recycling
As reported in Chapter 2, thermal recycling technology mainly includes pyrolysis, fluidized bed recycling process and microwave pyrolysis. As the load transfer capability in polymer composites is strongly dependent both on the intrinsic mechanical properties of the reinforcing fibers and on the interfacial shear strength, the latter aspect should be taken into account also in recycled FRPs. In a recent work of Rahimizadeh, et al., both thermal and mechanical recycling methods were considered to reclaim glass fibers from end-of-life wind turbine blades [28]. WT blades were cut in small pieces and then grinded through a hammer mill, the resulting materials were then sieved with a screen classifier of 19 mm. The thermal recycling process was performed in a pyrolysis furnace at 550 °C for 45 min under a nitrogen atmosphere, followed by an oxidation at the same temperature for 10 min, in order to remove residual ashes on the fiber surface. SEM micrographs of the recycled and virgin fibers are shown in Figure 4(a-c). It is evident that mechanically recycled fibers were characterized by a higher surface roughness, because of the presence of epoxy residues deriving from the grinding process, while pyrolyzed and virgin glass fibers presented a smoother profile. As it could be expected, virgin fibers presented the highest stress at break, i.e. 20% higher than mechanically recycled GFs and 60% higher than pyrolyzed ones. Interestingly, elastic modulus of pyrolyzed fibers was 17% higher than that of the grinded ones. For as concerns the interfacial bonding strength, mechanically recycled fibers showed the highest apparent interfacial shear strength (IFSS), i.e. 13 MPa, that was respectively 14% and 26% higher than that of pyrolyzed and virgin glass fibers.
Figure 4. SEM images of the surface morphology of different GFs: (a) ground fibers, (b) pyrolyzed fibers and (c) virgin fibers [28].
3.3 Chemical recycling
Chemical recycling technology is based on the chemical decomposition of the matrix to recover both the reinforcing fibers and some degradation products, that could be utilized to prepare fresh polymeric materials or other valuable chemicals. Even if at the beginning chemical recycling methods were mainly focused in the recovery of only the fibrous reinforcements, recently, many studies have demonstrated that decomposing thermosetting resins in mild conditions it is possible to recover also low molecular weight oligomers for high value added applications [29]. Even if at a general level the recycling effect is better, these methods applied to thermoset composites are technically difficult and quite expensive. Nowadays, the most interesting chemical recycling methods are the solvolysis and the use of supercritical fluids.
As reported in Chapter 2, through solvolysis it is possible to depolymerize the resin by using a proper solvent and temperature. Through this method it is possible to obtain an efficient recovery of both the fibers and the resin, but the solvents generally utilized are toxic and expensive. Among the most important European projects financed by the EU on the recycling of FRPs, the EURECOMP project was specifically devoted to the recycling of thermosetting composites through solvolysis [30], in order to recover the fibres as a valuable reinforcement in new composites, and to obtain from the matrix precious precursors for the chemical industry. On the other hand, super/subcritical fluid recycling technology is a promising clean and environmental friendly process, that allows the recovery of fibers with clean surface and good mechanical properties. However, the temperature and pressure conditions are often rather heavy, and expensive equipment is often required. Because of these reasons, the recovery of thermosetting resin composites by supercritical fluid technology is still in the laboratory stage [23].
Considering that chemical recycling technologies are at the beginning of their development stage, it is not easy to find in literature specific works devoted to the chemical recycling of thermosetting composites recovered from wind blades. The Danish innovation consortium GENVIND, active between 2012 and 2016, tried to give an overview on the different recycling methods for wind turbines and to propose secondary applications [30]. In this project, both the solvolysis below supercritical conditions (through nitric acid, ammonia or glycol at temperature below 100 °C and/or pressure lower than 1 bar) and the supercritical fluid recycling (through water or ethanol) were considered. It was concluded that many of these recycling methods are highly specialized, and this aspect puts a serious limit to where it is being offered and how widespread it can be. Moreover, the feasibility of these processes is limited also because they are generally time and energy demanding. This is the main reason why the greatest part of the chemical recycling processes are still at a lab-scale or pilot-scale level, and their full-scale efficacy has not yet verified.
4. Innovative solutions for composite blades with improved recyclability
On the basis of the information reported in the previous chapters, it emerges that both GF and CF reinforced thermoset composites are difficult to be effectively recycled, and in some cases they have high recycling cost. Therefore, researchers have conducted many studies on novel recyclable composite materials, to be applied also in the wind industry. At present, FRPs with improved recyclability mainly include modified thermosetting composites, thermoplastic composites and natural fiber composites [23].
4.1 Modified thermosetting composites
Considering that thermosetting polymers are generally infusible and insoluble, many efforts have been recently devoted to introduce active covalent bonds in epoxy systems. Under external stimuli such as light, heat and irradiation, the breaking and recombination of covalent bonds can be obtained. In other words, covalent adaptable networks (CANs) can be utilized for mending or self-healing, for the activation of shape change or stress reduction mechanisms, and for recycling/reprocessing thermosetting polymers. In the latter case, an epoxy matrix could be reshaped and reprocessed like a thermoplastic. At a general level, CANs can be divided in two categories, depending if the dynamic macromolecular structure can be obtained through bond exchange or through equilibrium shifts leading to reversible depolymerization.
In CANs systems belonging to the first category, exchangeable bonds are subjected to cleavage and reformation, and thus the total number of bonds (i.e. the crosslinked structure and the original stiffness of the matrix) is retained [31]. CANs based on addition-fragmentation chain transfer (AFT) capable moieties, like allyl sulfides or trithiocarbonates, have been recently developed. The thiyl radical-mediated addition–fragmentation of an allyl sulphide could be an example of CANs based on AFT reactions (see Figure 5). In these systems, the generation of radical species and thus the bond exchange reactions can be realized through the exposure to light, thanks to the action of a radical-based photoinitiator. For instance, photoinduced repeatable self-healing of covalently crosslinked structures through re-organization of photoresponsive trithiocarbonate (TTC) units was reported by Amamoto et al. [32].
Figure 5. An example of the thiyl radical-mediated addition-fragmentation of an allyl sulphide [31].
The second category of CAN systems is based on thermoreversible bond structures in which, thanks to the presence of Diels-Alder adducts, polymerization-depolymerization reactions occur [33]. For instance, the equilibrium Diels-Alder adduct reaction between a furan-based diene and a maleimide-based dieneophile determines the formation of crosslinked structures at low temperature and the depolymerization upon heating. In these conditions, the reprocessing and/or the crack healing of the polymer matrix can be performed at elevated temperatures.
A new generation of hardeners for epoxy resins, called Recyclamines®, have been recently proposed by Connora Technologies, with the aim to develop recyclable thermosets which can be easily converted into reprocessable thermoplastics. Therefore, epoxy hardeners derived from polyamine structures, in which amino end groups can be tethered together by a central cleavable group, were prepared. In order to induce crosslinks cleavage in the epoxy network and obtain a thermoplastic molecular structure, a combination of elevated temperature (70-100 °C) and pH (acidic conditions) are required. In these conditions, starting from equimolar mixtures of bisphenols and epichlorohydrin, true thermoplastics can be produced [34]. Depending upon the bisphenol utilized for the synthesis, a wide variety of amorphous, moldable matrices, called poly(-hydroxyethers) or phenoxy resins, can be produced, having glass transition temperatures (Tg) from 80 to 175 °C.
4.2 Thermoplastic composites
Nowadays thermoplastic composites find large application in aerospace and automotive sectors, but they started to be considered in the wind industry only after 2005. The interest towards thermoplastic matrices derives from the need to dismantle the first batch of service blades and from the consequent abandonment of a large number of blade materials, that could be hardly recycled [35]. Moreover, thermoplastic composites could be interesting because they are endowed with shorter and cheaper manufacturing cycle times.
As already reported in Chapter 2, composite materials are generally characterized by elevated embodied energy values, and thus recovery of their constituents can lead to considerable economic and environmental advantages [36]. Moreover, the possibility of reclaiming both the matrix and full-length fibers at the end of life through dissolution of the thermoplastic phase at low temperatures could be an interesting option to re-introduce recovered materials into the supply chain. For instance, Brown et al. analysed the structural performances of a vertical axis thermoplastic composite WT blade constituted by a sandwich structure with commingled woven GF/PP thermoplastic composite skins and a polyethylene terephthalate (PET) foam core [37]. Garate et al. investigated the possibility to produce WT blades based on a PP matrix with 65% E-glass fibers [38]. In the paper of Nat et al., 30% CF/polyether ether ketone (PEEK) thermoplastic composite was utilized as plying material for WT blades [35].
The production of traditional thermosetting composite WT blades is generally performed through vacuum infusion processes but, due to their elevated viscosity at the molten/softened state, thermoplastic polymers are not suitable to be processed in this way. In order to overcome this limitation, novel low viscosity thermoplastic solutions, processable with liquid moulding technologies and possessing good thermo-mechanical properties, have been recently developed. In these systems, the liquid monomer of a thermoplastic matrix is infiltrated together with an activator in the woven fabric of the reinforcement. Polymerization reaction can then take place within the fiber bed, obtaining thus a thermoplastic FRP.
Different thermoplastic composites with low viscosity polyamide based systems have been recently developed. An anionic polylactam 12 (APLC12), precursor of polyamide 12 (PA12), has been proposed by EMS Chemie AG. Tailoring the initiator and the reaction temperature, it is possible to perform PA12 polymerization from few seconds to several minutes, and also composites with elevated fiber concentration can be impregnated [39]. Moreover, the prepared material showed a very limited shrinkage during polymerization and were characterized with a void concentration below 1%. Rijswijk et al. synthesized an anionic polyamide 6 (APA6) starting from a carbamoylcaprolactam activator (see reaction scheme in Figure 6) [40]. Moreover, the surface chemistry and morphology of the reinforcing fibers were modified to improve the interfacial adhesion with APA6 matrix. It was demonstrated that increasing the moulding temperature a stronger interfacial bonding could be obtained, but the crystallinity degree of the matrix was reduced, therefore a compromise between these two effects was necessary. It was also shown that a stronger interaction of the activators with the fibers did not necessary increase the mechanical performance of the material.
Figure 6. Anionic polymerization of caprolactam into polyamide 6 using a carbamoylcaprolactam activator [41].
Among innovative flowable thermoplastic resins for thermoplastic FRPs, also cyclic butylene terephthalate (CBT), precursor of poly(butylene terephthalate) (PBT), was considered [42]. In a paper of Ishak et al., cyclic butylene terephthalate (CBT) has been polymerized in situ at T = 190 °C both in the presence and absence of woven glass fabrics. The thermal properties of the in situ polymerized PBT were compared with those of a commercial injection moulded PBT. It was found that the crystallinity of the injection moulded PBT was significantly lower than that of the in situ synthesized one, that was thus more brittle. In situ polymerized composites reinforced with GFs at a concentration of 50 vol% were prepared by compression moulding at 190 °C, and SEM images highlighted a good interfacial fiber-matrix bonding. For this reason, this formulation was utilized to produce for the first time recyclable wind turbine blades with a length of 12.6 m.
In a recent paper of Cousins et al. the possibility of recycling a spar cap of a WT blade prepared with a GF reinforced Elium® thermoplastic matrix was shown [43]. Elium® is a liquid thermoplastic resin belonging to the family of methacrylates, that could be applied in infusion processes. Thanks to the presence of a peroxide initiator, it can be polymerized at high temperature and converted in a solid thermoplastic polymer [44]. Interestingly, polymerized Elium® resin can be dissolved in chloroform and recovered in methanol, recovering thus in recycling operations both the matrix and full-length GFs.
4.3 Natural fiber composites
Nowadays GFs dominate the market of the fibers for composite materials, and in 2015 about the 95% of the composites were reinforced with this material. Due to the increasing environmental concerns on the use of non-renewable resources, an increasing attention has been recently paid on the replacement of traditional reinforcing materials with natural biodegradable fibers [45]. Natural fibers such as flax, coir and bamboo are easily available and are characterized by low processing costs. Natural fiber reinforced composites (NFRCs) present some advantages over synthetic fiber reinforced laminates, like low density, limited cost and biodegradability. Also natural fiber reinforced composites can be grinded at their end of life, re-impregnated and re-utilized in an open loop recycling perspective, but probably the most attractive option for these materials is their biodegradation. According to the Natural Fiber Composites Market forecasts, it is expected that global NFRCs market size will increase from $4.46 billion in 2016 up to $10.89 billion by 2024, thanks also to the need of lightweight and fuel-efficient vehicles [46]. On the other hand, the most heavy limitations in the further expansion of NFRCs are represented by some intrinsic features of natural fibers, like their variable quality and limited mechanical properties, their water absorption tendency and limited thermal stability. Moreover, they are incompatible with hydrophobic matrices and often tend to agglomerate. In literature, it is possible to find recent reviews about the last developments on NFRCs [46-48]. Both thermoplastic and thermosetting resins can used as matrices for natural fibers. Because most natural fibers are not thermally stable above 200 °C, only polymer matrices that can be processed below this temperature can be utilized (i.e. PP, low density polyethylene (LDPE), high density polyethylene (HDPE) and PLA). Quite surprisingly, only few works dealing with degradation mechanisms of NFRCs under light or environmental exposure or under the attack of fungi and microbial agents can be found in literature. These factors should be crucial design parameters in NFRCs, as natural fibers can easily degrade on the biological, photochemical and aqueous environment. These tests were mainly performed only on thermoplastic composites with biodegradable matrices (like PLA), and many attempts have been recently made to improve the biodegradability of NFRCs through modification of the matrix and of the reinforcing fibers [48].
5. Conclusions and future perspectives
Considering the increasing number of end of life WT blades and the recent concerns on resource conservation and environmental protection, growing attention has been paid to the recycling of thermosetting FRPs for wind turbine blades.
Mechanical recycling is economically feasible and probably represents the most mature technology, but inevitably leads to a general downgrading of the recycled products and thus to the production of secondary components for non-structural and lower value applications. Moreover, new markets for mechanically recycled composites needs to be detected, and virgin continuous reinforcing fibers (and new resin) for the production of new WT blades, replacing the dismantled ones, are required. In this sense, the environmental sustainability of this process is questionable. Pyrolytic processes (with or without microwave application) seem to represent an interesting option for the recycling of composite blades, and some examples of commercial application of this technology can be found on the market. Even in this case, the problems related to the discontinuous morphology of the recovered fibers and the need to find new market applications for the chemicals derived from the pyrolysis need to be carefully analyzed. At the present state chemical recycling, due to the use of hazardous chemicals/solvents and harsh processing conditions, does not represent a feasible solution for a full scale recovery of waste composites in the wind energy market. However chemical recycling through supercritical fluids, involving the use of environmentally friendly substances, could be an interesting option, if an adequate upscaling of this technology will be realized. Considering the issues related to the recycling of traditional thermosetting composites, more attention should be probably paid in the future to recyclable and environmentally friendly composite blade materials. The possibility to use modified thermosetting resins, that could be processed like a traditional epoxy resin and that could be recycled like thermoplastics, if heaten or irradiated, represents an interesting option for the future. In this case, the heaviest problem is represented by the limited number of matrices that are actually available on the market and their cost. The possibility to use thermoplastic composites for wind blades, constituted by low viscosity precursors that could be applied through resin infusion, probably represents one of the most promising perspectives for the future wind blade technology. On the other hand, the development of composite blades with natural fibers embedded in biodegradable matrices could be interesting both for the reduction of the embedded energy related to the blade production and for the possibility to dispose of the components through biodegradation after the end of life. In this case, the problems related to the constancy of the thermo-mechanical properties of the reinforcements and to the water absorption of biodegradable matrices should be overcome.
6. References
[1] I. Al Bahadly, Wind Turbines, InTech, Rijeka (Croatia), 2011.
[2] IRENA renewable capacity statistics (2019).
[3] AWEA, Small Wind Global Market Study, Washington DC (USA), 2010.
[4] Renewable_UK, Small Wind Systems: UK Market Report, London (UK), 2010.
[5] NRC, Electricity from Renewable Resources: Status, Prospects and Impediments, National Academies Press, Washington DC (USA), 2010.
[6] C.G. Anderson, Wind Turbines - Theory And Practice, Cambridge University Press, Cambridge (UK), 2020.
[7] V. Goodship, Management, Recycling and Reuse of Waste Composites, Woodhead Publishing Ltd, Cambridge (UK), 2010.
[8] S.J. Pickering, Recycling technologies for thermoset composite materials—current status, Compos. Part A Appl. Sci. Manuf. 37 (8) (2006) 1206-1215.
[9] R.A. Witik, R. Teuscher, V. Michaud, C. Ludwig, J.A.E. Månson, Carbon fibre reinforced composite waste: An environmental assessment of recycling, energy recovery and landfilling, Compos. Part A Appl. Sci. Manuf. 49 (2013) 89-99.
[10] M.F. Ashby, Materials and the Environment - Second Edition, Elsevier, 2013.
[11] M. Prinçaud, C. Aymonier, A. Loppinet-Serani, N. Perry, G. Sonnemann, Environmental Feasibility of the Recycling of Carbon Fibers from CFRPs by Solvolysis Using Supercritical Water, ACS Sustain. Chem. Eng. 2 (6) (2014) 1498-1502.
[12] S. Pimenta, S.T. Pinho, Recycling of Carbon Fibers. In: E. Worrell, M. Reuter (Eds.), Handbook of Recycling, Elsevier, 2014, pp 269-283.
[13] A. Conroy, S. Halliwell, T. Reynolds, Composite recycling in the construction industry, Compos. Part A Appl. Sci. Manuf. 37 (8) (2006) 1216-1222.
[14] C.E. Kouparitsas, C.N. Kartalis, P.C. Varelidis, C.J. Tsenoglou, C.D. Papaspyrides, Recycling of the fibrous fraction of reinforced thermoset composites, Polym. Compos. 23 (4) (2002) 682–689.
[15] S. Pimenta, S.T. Pinho, The effect of recycling on the mechanical response of carbon fibres and their composites, Compos. Struct. 94 (12) (2012) 3669-3684.
[16] R. De Rosa, E. Telfeyan, J.S. Mayes, Current state of recycling sheet molding compounds and related materials, J. Thermoplast. Compos. Mater. 18 (3) (2005) 219–240.
[17] I. Okajima, T. Sako, Recycling of carbon fiber reinforced plastic using supercritical and subcritical fluids, J. Mater. Cycles Waste Manag. 19 (2015) 15-20.
[18] R. Pinero Hernanz, C. Dodds, J. Hyde, J.G. Serna, M. Poliakoff, E. Lester, M.J. Cocero, S. Kingman, S. Pickering, K.H. Wong, Chemical recycling of carbon fibre reinforced composites in nearcritical and supercritical water, Compos. Part A Appl. Sci. Manuf. 39 (2008) 454–461.
[19] J.R. Hyde, E. Lester, S. Kingman, S. Pickering, K.H. Wong, Supercritical propanol, a possible route to composite carbon fibre recovery: a viability study, Compos. Part A Appl. Sci. Manuf. 37 (2006) 2171–2175.
[20] R. Pinero-Hernanz, J.G. Serna, C. Dodds, J. Hyde, M. Poliakoff, M.J. Cocero, S. Kingman, S. Pickering, E. Lester, Chemical recycling of carbon fibre composites using alcohols under subcritical and supercritical conditions, J. Supercrit. Fluids 46 (2008) 83–92.
[21] G. Jiang, S. Pickering, E. Lester, T.A. Turner, K.H. Wong, N.A. Warrior, Characterisation of carbon fibres recycled from carbon fibre/epoxy resin composites using supercritical n-propanol, Compos. Sci. Technol. 69 (2009) 192–198.
[22] K.H. Wong, T.A. Turner, S.J. Pickering, N.A. Warrior, The potential for fibre alignment in the manufacture of polymer composites from recycled carbon fibre, SAE AeroTech Congress and Exhibition (SAE International), Seattle (USA), 2009
[23] J. Chen, J. Wang, A. Ni, Recycling and reuse of composite materials for wind turbine blades: An overview, J. Reinf. Plast. Compos. 38 (12) (2019) 567-577.
[24] R. Cherrington, V. Goodship, J. Meredith, B.M. Wood, S.R. Coles, A. Vuillaume, A. Feito-Boirac, F. Spee, K. Kirwan, Producer responsibility: Defining the incentive for recycling composite wind turbine blades in Europe, Energy Policy 47 (2012) 13-21.
[25] J. Petterson, P. Nilsson, Recycling of SMC and BMC in standard processing equipment, J. Thermoplast. Compos. Mater. 7 (1) (1994) 56-63.
[26] J. Beauson, H. Lilholt, P. Brøndsted, Recycling solid residues recovered from glass fibre-reinforced composites – A review applied to wind turbine blade materials, J. Reinf. Plast. Compos. 33 (16) (2014) 1542-1556.
[27] A. Rahimizadeh, J. Kalman, R. Henri, K. Fayazbakhsh, L. Lessard, Recycled Glass Fiber Composites from Wind Turbine Waste for 3D Printing Feedstock: Effects of Fiber Content and Interface on Mechanical Performance, Materials 12 (23) (2019).
[28] A. Rahimizadeh, M. Tahir, K. Fayazbakhsh, L. Lessard, Tensile properties and interfacial shear strength of recycled fibers from wind turbine waste, Compos. Part A Appl. Sci. Manuf. 131 (2020) 105786.
[29] S. Kumar, S. Krishnan, Recycling of carbon fiber with epoxy composites by chemical recycling for future perspective: a review, Chem. Zvesti. 74 (11) (2020) 3785-3807.
[30] J.P. Jensen, K. Skelton, Wind turbine blade recycling: Experiences, challenges and possibilities in a circular economy, Renew. Sust. Energ. Rev. 97 (2018) 165-176.
[31] C.N. Bowman, C.J. Kloxin, Covalent adaptable networks: reversible bond structures incorporated in polymer networks, Angew. Chem. Int. Ed. 51 (18) (2012) 4272-4274.
[32] Y. Amamoto, J. Kamada, H. Otsuka, A. Takahara, K. Matyjaszewski, Repeatable Photoinduced Self-Healing of Covalently Cross-Linked Polymers through Reshuffling of Trithiocarbonate Units, Angew. Chem. 123 (7) (2011) 1698-1701.
[33] X.X. Chen, M.A. Dam, K. Ono, A. Mal, H.B. Shen, S.R. Nutt, K. Sheran, F. Wudl, A Thermally Re-mendable Cross-Linked Polymeric Material, Science 295 (2002) 1698 – 1702.
[34] J.E. White, H.C. Silvis, M.S. Winkler, T.W. Glass, D.E. Kirkpatrick, Poly(hydroxyaminoethers): A New Family of Epoxy-Based Thermoplastics, Adv. Mater. 12 (23) (2000) 1791-1800.
[35] R. Na, H. Zhai, H. Cen, Layer design and fluid-solid coupling analysis of the thermoplastic composite wind turbine blade, Int. J. Performability Eng. 14 (12) (2018) 2927-2940.
[36] S.S. Yao, F.L. Jin, K.Y. Rhee, D. Hui, S.J. Park, Recent advances in carbon-fiber-reinforced thermoplastic composites: A review, Compos. B. Eng. 142 (2018) 241-250.
[37] K.A. Brown, R. Brooks, Design and analysis of vertical axis thermoplastic composite wind turbine blade, Plast. Rubber Compos. 39 (3-5) (2010) 111-121.
[38] J. Garate, S.A. Solovitz, D. Kim, Fabrication and Performance of Segmented Thermoplastic Composite Wind Turbine Blades, Int. J. Precis. Eng. Manuf. 5 (2) (2018) 271-277.
[39] L. Zingraff, V. Michaud, P.E. Bourban, J.A.E. Månson, Resin transfer moulding of anionically polymerised polyamide 12, Compos. Part A Appl. Sci. Manuf. 36 (12) (2005) 1675-1686.
[40] K. Van Rijswijk, S. Joncas, H.E.N. Bersee, O.K. Bergsma, A. Beukers, Sustainable vacuum-infused thermoplastic composites for MW-size wind turbine blades - Preliminary design and manufacturing issues, J. Sol. Energy Eng. 127 (4) (2005) 570-580.
[41] K. Van Rijswijk, J.J.E. Teuwen, H.E.N. Bersee, A. Beukers, Textile fiber-reinforced anionic polyamide-6 composites. Part I: The vacuum infusion process, Compos. Part A Appl. Sci. Manuf. 40 (1) (2009) 1-10.
[42] Z.A. Mohd Ishak, Y.W. Leong, M. Steeg, J. Karger-Kocsis, Mechanical properties of woven glass fabric reinforced in situ polymerized poly(butylene terephthalate) composites, Compos. Sci. Technol. 67 (3-4) (2007) 390-398.
[43] D.S. Cousins, Y. Suzuki, R.E. Murray, J.R. Samaniuk, A.P. Stebner, Recycling glass fiber thermoplastic composites from wind turbine blades, J. Clean. Prod. 209 (2019) 1252-1263.
[44] G. Fredi, A. Dorigato, A. Pegoretti, Novel Reactive Thermoplastic Resin as a Matrix for Laminates Containing Phase Change Microcapsules, Polym. Compos. 40 (2019) 3711-3724.
[45] M.D.H. Beg, K.L. Pickering, Mechanical performance of Kraft fibre reinforced polypropylene composites: Influence of fibre length, fibre beating and hygrothermal ageing, Compos. Part A Appl. Sci. Manuf. 39 (11) (2008) 1748-1755.
[46] M. Li, Y. Pu, V.M. Thomas, C.G. Yoo, S. Ozcan, Y. Deng, K. Nelson, A.J. Ragauskas, Recent advancements of plant-based natural fiber–reinforced composites and their applications, Compos. B. Eng. 200 (2020) 108254.
[47] M. Syduzzaman, M.A. Al Faruque, K. Bilisik, M. Naebe, Plant-Based Natural Fibre Reinforced Composites: A Review on Fabrication, Properties and Applications, Coatings 10 (10) (2020) 973.
[48] S. Vigneshwaran, R. Sundarakannan, K.M. John, R.D. Joel Johnson, K.A. Prasath, S. Ajith, V. Arumugaprabu, M. Uthayakumar, Recent advancement in the natural fiber polymer composites: A comprehensive review, J. Clean. Prod. 277 (2020) 124109.