Upgrading the household plastic waste: the case of PET and plasmix
Marco Aldo Ortenzi, Stefano Gazzotti, a Marco Parolini, Beatrice De Felice, Cristian Gambarotti, Ada Truscello
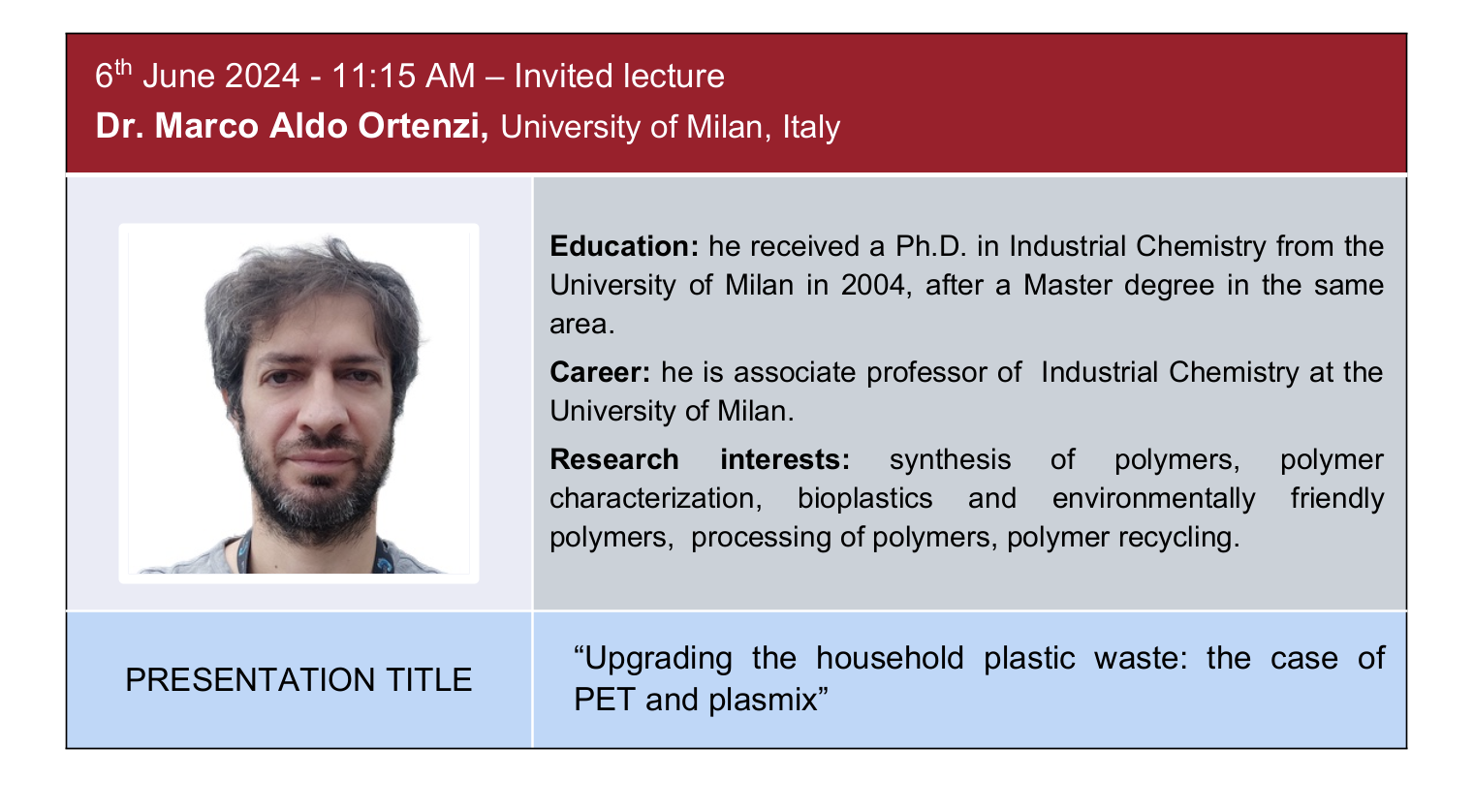
Italy is one of the leading countries in EU in the recycling of household plastic waste, with a recycling rate of 48.9% of all plastics put on the market in 2022: recycling is almost exclusively mechanical, with chemical recycling accounting only for 1.719 tons [1]. When dealing with household plastic waste the polymers involved are mainly polyolefines (PE, PP, PS) and PET. PET is the “perfect” polymer for recycling, being used for food packaging in bottles, trays etc, generally with little or no additives. Moreover, the PET grade used is the same for the different applications, making the waste highly homogeneous and therefore valuable. Unfortunately, PET suffers high processing temperatures therefore it tends to downgrade when transformed in new objects. This makes its direct recycling (i.e. the “bottle to bottle”) hard: a common approach used to achieve it relies in the use of multifunctional additives, that during extrusion partially react with PET increasing its molecular weight. Examples of additives commonly used are Joncryl® family by BASF or pyromellitic Dianhydride (PMDA): both are oil-based. Given the huge production volumes of PET and the push for recycling, the total quantity of additives used worldwide is quite high and this poses a serious environmental concern. If PET is the “perfect” polymer for recycling, there is a big fraction of plastic waste, the so-called plasmix, composed by heterogeneous wastes (ex. multilayer materials) that currently cannot be recycled and is mostly destined to energy recovery. In 2022 the Italian plasmix accounts for about 550 ktons. It is therefore evident that finding a way to efficiently recycle plasmix, possibly upgrading it to higher value applications, would be high beneficial environmental impact. This presentation illustrates two strategies aimed to upgrading both R-PET and plasmix. In the case of PET, a new 100% biobased reactive additive, mellophanic dianhydride (MEDA), was synthesized and tested in extrusion with R- PET [3]. Injection molded specimens were obtained and tested in comparison to R-PET alone. Results show that in the blow molding region temperature (i.e. 90-110°C), Young’s modulus of R- PET+0.5%MEDA is 20% higher than that of R-PET alone (Fig. 1).
In the case of plasmix, a polyacrilate was synthesized, acting as compatibilizer between the polymeric phases present. The compatibilizer was tested in extrusion with a plasmix. Injection molded specimens were obtained and compared with plasmix alone and with a plasmix containing an industrial phase compatibilizer (Fig. 2).
Results show that the acrylic compatibilizer gives higher modulus in almost all temperatures, proving effective in view of a potential upgrading of plasmix itself.
References
- COREPLA, Rapporto di sostenibilità 2022
- A. Truscello, S. Colletti, C. Gambarotti, M.A. Ortenzi, S. Gazzotti, M. Galimberti ACS Sustainable Chem. Eng. 2023, 11, 9721
Acknowledgments
Fundings: FONDAZIONE CARIPLO, project “PHOENIX—Push for a second valuable life to Plasmix”, grant number CAR_RIC20MPARO_01 and MUSA – Multilayered Urban Sustainability Action – project, funded by the European Union – NextGenerationEU, under the National Recovery and Resilience Plan (NRRP) Mission 4 Component 2 Investment Line 1.5: Strenghtening of research structures and creation of R&D “innovation ecosystems”, set up of “territorial leaders in R&