What is the difference between thermoplastic and thermoset polymers?
Thermoplastics are polymers that become soft when heated and hard when cooled.
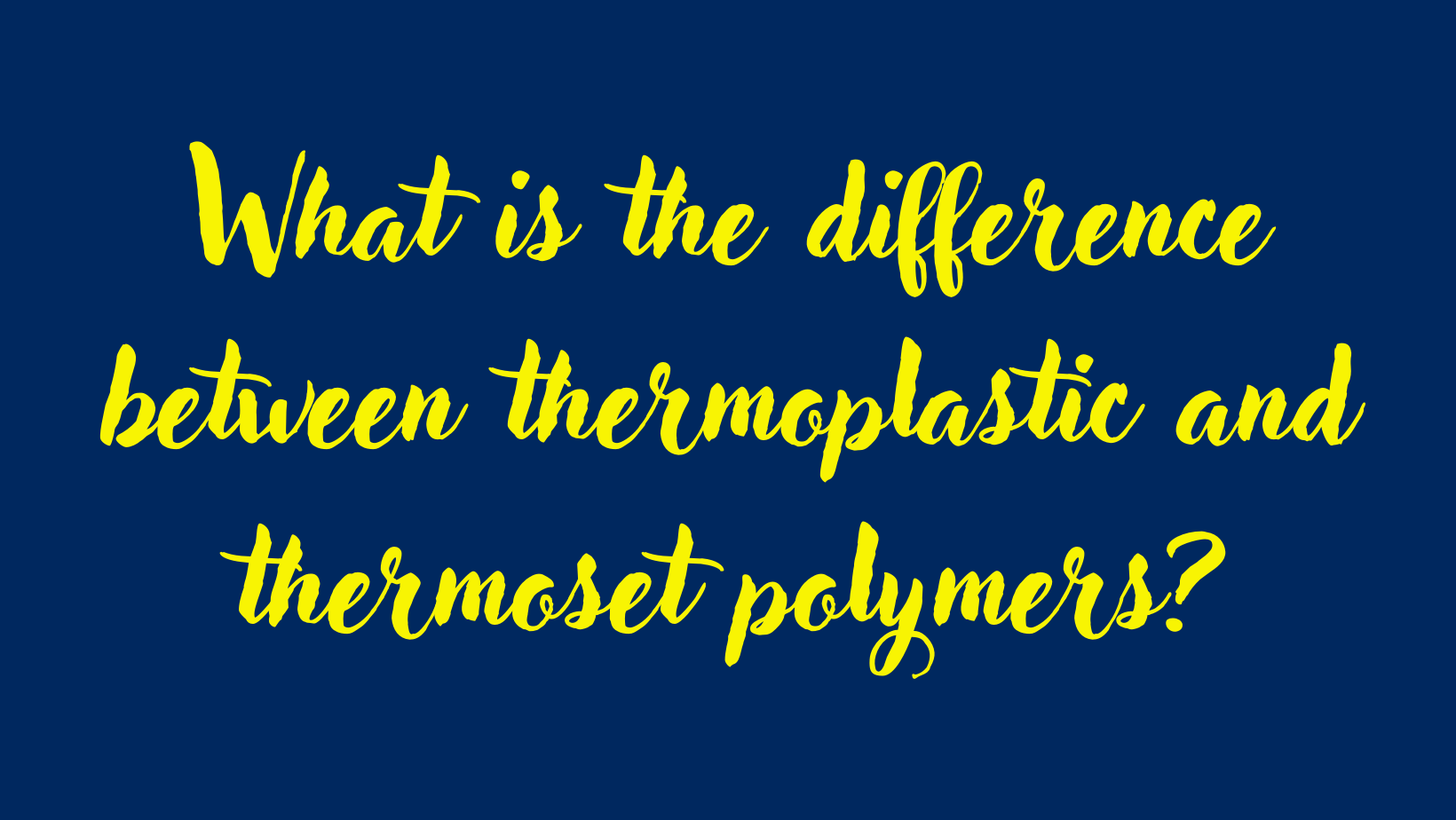
When heated above specific threshold temperatures, thermoplastics become homogeneous liquids and, in this state, they can be reshaped and resized by different processing techniques. Thermoplastics are easily recycled, since the solid-liquid transition is reversible and can in principle take place multiple times without significantly affecting the material’s properties.
Thermoplastics account for about 76% of the global consumption of plastics. The share of the regional consumption of major thermoplastics for north America, Western Europe and China, is reported in the Figure 1 [Michel Biron, in Material Selection for Thermoplastic Parts, 2016].
Figure 1: Regional consumption of thermoplastics.
Thermosets are a class of polymers that form well-defined, irreversible, chemical networks that grows along 3D directions through the process of curing or hardening. This process causes the cross-linking of polymer chains and can occur either due to heating or through the addition of a curing agent. The result is a strong and rigid structure that can be added to other materials to increase strength.
About 69% of the application of thermosets are in building and construction, other uses of thermosets are in transport, adhesives and electrical equipment. Thermosets are also widely used in advanced applications for aerospace and military industries, especially when they include reinforcing agents such as carbon and glass fibers.
Comparison between thermoplastics and thermosets at the molecular level
Figure 2: Molecular structure of thermoplastics and thermosets.
Thermoplastics are made of individual macromolecules, whereas in thermosets macromolecules are chemically cross-linked through covalent bonds.